Kolchiko – Lagadas
About the site
The Biogas Lagadas S.A. (BLAG) plant is located in Kolchiko – Lagadas, in the Central Macedonia Region.
The BLAG plant exploits around 80,000 tonnes of livestock waste per year, yielding 8,400 MWh of electricity and 75,000 tonnes of organic soil improver suitable for fertilizing 5,000 acres of agricultural land.
The plant has a capacity of 290 m³ CH4/h. The BLAG’s biogas plant has 2 fermenters with 4,500 m3 active volume for biomass (each one) and 10,000 m3 of biogas buffer capacity.
The total flow is 500 Nm³/h at 100 mbar. The CHP generator produces 1MWel/h.
Our technology in brief
The technology concerns the conversion of CO2 contained in the biogas to biomethane, through its reaction with renewable hydrogen in a catalytic reactor.
The catalytic reactor can handle a mixture of methane and carbon dioxide (raw biogas); thus, no separation of the biogas is required before conversion. The reaction takes place at high pressure and temperature. The individual stages of the whole process include: (1) a cleaning and compressing step of the biogas, (2) the catalytic methanation reactor, and (3) the dehumidification of the final biomethane stream. The final product is biomethane already reaching pipeline quality gas standards (e.g., 96-98 vol-% CH4), requiring no further upgrading.
Our ambition
The technology will be transferred for first time to biogas application at TRL 7. In specific, a catalytic technology will be integrated into the industrial LAGADA biogas plant. A t-type joint connection will be providing the proper flow to the pilot reactor. The produced biomethane will meet the requirements of pipeline quality (96-98 vol-% CH4). Τhe target is to produce a total of 15,000 m3 of biomethane. The input biogas flow will be 6 Nm3/h, while the output flow of the upgrading unit will yield an additional 2.4 Nm3/h biomethane corresponding to the conversation of CO2 stream into biogas stream. The CH4 contained into biogas stream (3.5 Nm3/h) will be incorporated in the output flow as well. Hence, via the thermochemical/catalytic methanation, the methane content will be increased from 60% in the input stream towards more than 95% in the output stream. The aim is to operate the pilot plant a total of 6,000 hours. The target for the total energy efficiency of the process is 61%, defined as the energy content of the biomethane produced divided by the electricity consumption to produce renewable hydrogen by electrolysis.
Our challenges
The most attractive configuration for the methanation section will be identified taking into consideration several factors, including but not limited to heat exchange, catalyst type, process temperature and pressure. Essential aspects which must be considered amongst others are:
- catalyst deterioration and contamination
- safe distribution of H2 to the pilot unit and tank replenishment
- appropriate automation with the respective controller unit, and finally
- successful operation with regeneration cycles of the catalyst. The catalyst has been extensively tested for treatment of syngas produced from gasification process, so relevant protocols and step by step methodology have already been developed and to be used for the biogas case study at TRL 7.
In addition, renewable hydrogen has a significant contribution to the process. Hence, the accurate and secure handling and provision are considered critical for the implementation of the project. The basic engineering includes safety study for the hydrogen storage at biogas plant facilities, distribution through piping system to the upgrading plant and the blending stage. The hydrogen supply will be evaluated within the project.
Finally, the operation parameters, such as temperature, pressure, biogas composition will be controlled during the demo activities, in order to evaluate the process itself and recognizeany deviations (lower biomethane yield than the expected, lack of hydrogen, no ideal conditions for the catalyst). During the BIOMETHAVERSE project, all the aforementioned measures will be investigated to identify possible edge effects at scale for the transition of the biogas Lagada plant to a full scale biomethane production plant.
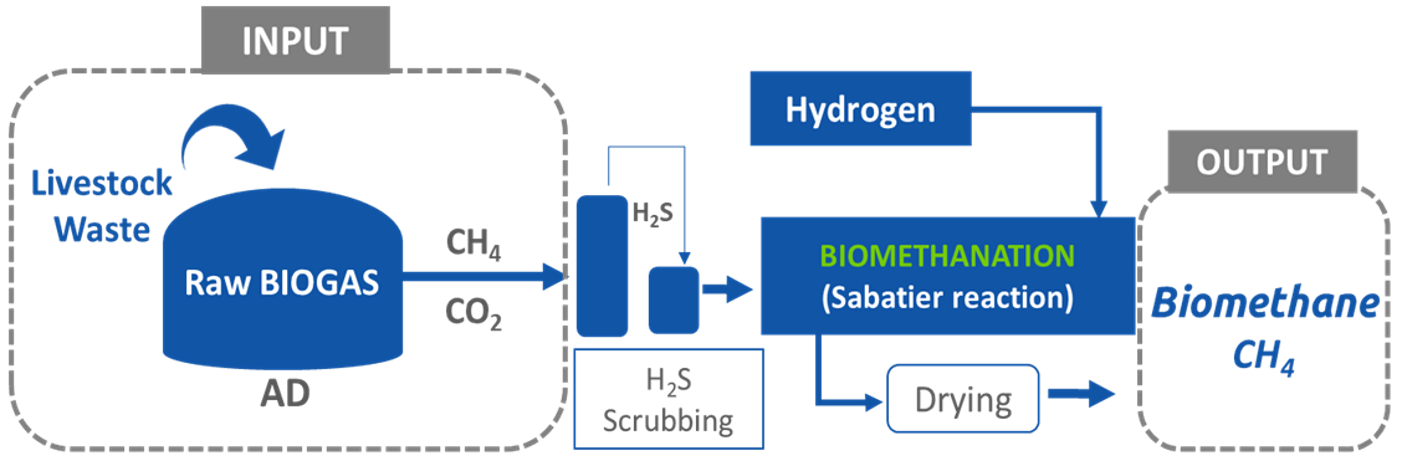